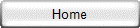
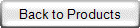
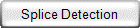
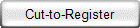
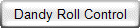
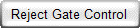
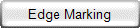
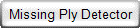
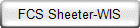
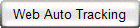
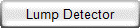
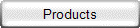
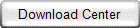
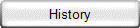
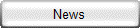
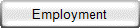
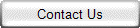
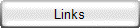
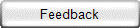
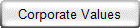
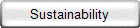
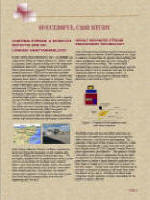
CASE STUDY
|
SPLICE DETECTOR SYSTEMS NEWS
Technology for Innovators, fix
the problem!
Leading Chinese
Paper Manufacturer Selects SDS Splice Detector Technology
- Splice Detector Technologies (SDS), the leader in
providing splice detection solutions worldwide has shipped a multi
order of its Model 1088 Sentinel™ Splice Detection Systems to a
leading Chinese paper manufacturer. The technology uses LV
technology coupled with proprietary signal processing to provide
100% detection of all known types of splices. The Sentinel
technology consumes very little power and is designed to monitor
multiple webs of material at a common pinch point and will detect
any splice or joint that may exist within the web based process. The
Sentinel will aid in the prevention of damage to sensitive equipment
such as soft rolls, Ink jet/laser print heads, coater applicators
and print blankets. Unaffected by printed surfaces, material color,
grade changes and process speeds that challenge “photo eyes” and
“ultrasonic devices”, the Sentinel guarantees 100% reliable
detection every day; every shift. Immediate detection, rejection and
control of splices or joints create savings of up to tens of
thousands of dollars per annum. The equipment will replace
unreliable technology currently in use on Jagenberg, ECH Will
sheeting type equipment.
Leading
Indonesian Paper Manufacturer Selects SDS Splice Detector Systems
- Splice Detector Technologies (SDS), the leader in
providing splice detection solutions worldwide has shipped a multi
order of its Model 1032B Classic™ Splice Detection Solutions to a
leading Indonesian paper manufacturer. This Splice Detector reveals
abrupt changes in web material thickness due to splices (paper
joints) in paper, coating and conversion processes. A single unit
will monitor multiple webs of material simultaneously for on-line
detection of splices. It automatically adjusts to changes in the #
of webs, type and caliper of materials. Special splice markings of
any kind are not required. Designed for center of web mounting, the
Model 1032B eliminates the need for repositioning to accommodate
changes in web width. It can be installed at any convenient position
in the web’s path to provide defect detection at the earliest
possible stage of the process. Both a signal contact closure and a
signal digital pulse output are included with each unit to
facilitate interfacing to control production equipment such as
sheeter gates, coating head applicators, presses, laminators,
treaters, audio/visual alarms as well as automatic marking systems.
The 1032B also be combined with a RKB Reject Gate Control Computer
or Multi-Color Automatic Edge Marking System for completely
unattended operation of your production equipment. The Model 1032B
guarantees 100% reliable detection every day; every shift. The
equipment will replace unreliable technology currently in use on
Jagenberg and ECH Will sheeting type equipment.
Leading
American coated webbing manufacturer invests in SDS Splice Detection
Technology
- Splice Detector Technologies (SDS), the leader in
providing splice detection solutions worldwide has shipped its Model
1088B Sentinel ™ Splice Detection Solution to a leading USA
manufacturer of coated webbing and assemblies, particularly in the
equine, national sports leagues to international space and military
organizational markets. A single unit will up to a total thickness
of 0.50” (12.7 millimeter). Unaffected by printed surfaces, material
color, grade changes and process speeds that challenge “photo eyes”
and “ultrasonic devices”, the Sentinel guarantees 100% reliable
detection every day; every shift. The Sentinel is a self-calibrating
system that is powered by 24VDC. It provides an opto-isolated,
digital electronic output with a pulse width selectable for 1, 10 or
100 milliseconds. The re-designed alarm indicators are low power,
low voltage LEDs that are clearly visible to machine attendants. The
unit can be mounted anywhere within the web at any angle and either
right side up or upside down. Our splice detector technologies are
designed for reliable, stable and consistent operation 24/7 in real
world conditions. Designed to operate on low speed through high
speed coating, laminating, printing, packaging and specialized
converting processes our splice detectors are proven the leader in
performance, reliability and price. Installations in over 150
Countries worldwide, join with leading manufacturers who demand
proven performance for their quality control initiatives.
Splice Detector
Technologies ships multiple systems to USA, Indonesia, Italy and the
United Kingdom
- Splice Detector Technologies (SDS), the leader in
providing splice detection technologies, has received orders for
multiple state-of-the-art splice detection systems worldwide. The
order will see shipment of our Model 1032 Classic™, Model 1088
Sentinel™ and Model 1032B Classic™ to four countries around the
world. A single unit will monitor multiple webs of material at a
common processing point. Unaffected by printed surfaces, material
color, grade changes and process speeds that challenge “photo eyes”
and “ultrasonic devices”, the technologies guarantee 100% reliable
detection every day; every shift. The systems can be mounted
anywhere within the web at any angle and either right side up or
upside down. Our splice detector technologies are designed for
reliable, stable and consistent operation 24/7 in real world
conditions. Designed to operate on low speed through high speed
coating, laminating, printing, packaging and specialized converting
processes our splice detectors are proven the leader in performance,
reliability and price. Installations in over 150 Countries
worldwide, join with leading manufacturers who demand proven
performance for their quality control initiatives.
Splice Detector
Technologies receives order from Leading Slovenia Paper Manufacturer
- Splice Detector Technologies (SDS), the leader in
providing splice detection solutions worldwide has shipped its Model
1032 Classic™ Splice Detection Solution to a leading Slovenia paper
manufacturer. This splice detection technology is applied too ensure
delivered product quality on many different grades of material such
as coated (i.e., silicone, release, adhesive, matt, gloss,
extrusion) papers, films, foils, rotogravure, flexographic,
holographic, non-wovens, textiles, tapes and specialty and writing
papers. The Model 1032 is self calibrating and will monitor multiple
webs of material simultaneously. No adjustments, settings or
re-calibrations are required. Our SST1032 is unaffected by material
basis weight changes, color or process speed, the unit automatically
adjusts itself to new conditions. Special splice tapes or color
marking are not required and the operation is unaffected by printed
material. Both a signal contact closure and a signal digital pulse
output are included with each unit to facilitate interfacing to
control production equipment such as sheeter gates, coating head
applicators, presses, laminators, treaters, audio/visual alarms as
well as automatic marking systems. The 1032 also be combined with a
RKB Reject Gate Control Computer or Multi-Color Automatic Edge
Marking System for completely unattended operation of your
production equipment. The Model 1032 guarantees 100% reliable
detection every day; every shift. The equipment will replace
unreliable technology currently in use on Jagenberg and ECH Will
sheeting type equipment.
Splice Detector
Technologies ships multiple systems within the USA
- Splice Detector Technologies (SDS), the leader in
providing splice detection technologies, has received orders for
multiple state-of-the-art splice detection systems within the United
States. The order will see shipment of our Model 1032 Classic™
Splice Detector Solution. A single unit will monitor multiple webs
of material at a common processing point. Unaffected by printed
surfaces, material color, grade changes and process speeds that
challenge “photo eyes” and “ultrasonic devices”, the technologies
guarantee 100% reliable detection every day; every shift. The
systems can be mounted anywhere within the web at any angle and
either right side up or upside down. Our splice detector
technologies are designed for reliable, stable and consistent
operation 24/7 in real world conditions. Designed to operate on low
speed through high speed coating, laminating, printing, packaging
and specialized converting processes our splice detectors are proven
the leader in performance, reliability and price. Installations in
over 150 Countries worldwide, join with leading manufacturers who
demand proven performance for their quality control initiatives.
Splice Detector
Technologies ships multiple systems to South East Asia and Europe
- Splice Detector Technologies (SDS), the leader in
providing splice detection technologies, has received orders for
multiple state-of-the-art splice detection systems. The order will
see shipment of our Model 1032 Classic™ and Model 1032B Classic™ to
Europe and South East Asia. A single unit will monitor multiple webs
of material at a common processing point. Unaffected by printed
surfaces, material color, grade changes and process speeds that
challenge “photo eyes” and “ultrasonic devices”, the technologies
guarantee 100% reliable detection every day; every shift. The
systems can be mounted anywhere within the web at any angle and
either right side up or upside down. Our splice detector
technologies are designed for reliable, stable and consistent
operation 24/7 in real world conditions. Designed to operate on low
speed through high speed coating, laminating, printing, packaging
and specialized converting processes our splice detectors are proven
the leader in performance, reliability and price. Installations in
over 150 Countries worldwide, join with leading manufacturers who
demand proven performance for their quality control initiatives.
Splice Detector
Technologies releases New Narrow Web Splice Detector Solution
- Splice Detector Technologies (SDS), the leader in
providing splice detection technologies has developed and released
its new narrow web splice detection solution. Designed for
implementation on narrow web processes such as ¼” to 4” wide lines,
this technology provides the same reliable detection capabilities as
its parent solutions. Unaffected by printed surfaces, material
color, grade changes and process speeds that challenge “photo eyes”
and “ultrasonic devices”, the technologies guarantee 100% reliable
detection every day; every shift. The systems can be mounted
anywhere within the web at any angle and either right side up or
upside down. Our splice detector technologies are designed for
reliable, stable and consistent operation 24/7 in real world
conditions. Designed to operate on low speed through high speed
coating, laminating, printing, packaging and specialized converting
processes our splice detectors are proven the leader in performance,
reliability and price. Installations in over 150 Countries worldwide
join with leading manufacturers who demand proven performance for
their quality control initiatives.
Splice Detector
Technologies receives order from Leading German Paper Manufacturer
- Splice Detector Technologies (SDS), the leader in
providing splice detection solutions worldwide has shipped its Model
1032B Classic™ Splice Detection Solution to a leading German paper
manufacturer. This splice detection technology is applied to ensure
delivered product quality on many different grades of material such
as coated (i.e., silicone, release, adhesive, matt, gloss,
extrusion) papers, films, foils, rotogravure, flexographic,
holographic, non-wovens, textiles, tapes and specialty and writing
papers. The Model 1032B is self-calibrating and will monitor
multiple webs of material simultaneously. No adjustments, settings
or re-calibrations are required. The 1032B is unaffected by material
basis weight changes, color or process speed, the unit automatically
adjusts itself to new conditions. Special splice tapes or color
marking are not required and the operation is unaffected by printed
material. Both a signal contact closure and a signal digital pulse
output are included with each unit to facilitate interfacing to
control production equipment such as sheeter gates, coating head
applicators, presses, laminators, treaters, audio/visual alarms as
well as automatic marking systems. The 1032B also be combined with a
RKB Reject Gate Control Computer or Multi-Color Automatic Edge
Marking System for completely unattended operation of your
production equipment. The Model 1032 guarantees 100% reliable
detection every day; every shift.
[
TOP PAGE ]
|